Helios Applied Systems key competency are in hand-eye coordination type processes. With know-how in robotics and image processing, Helios has develop proprietary integrated vision/motion robotic drive (VMD) system to deliver autonomous robotic solutions for industrial manufacturers. With this technology integrated into robotic cells, the vision system is able to,
1) Detect incoming part variations and in real-time
2) Drive the end-effector to positions with accuracy of less than 10 microns
3) Process parts that are floating (not jigged), with large incoming variations (e.g. repair parts) with high repeatability.
Leveraging on image processing expertise, Helios has develop the image base inputs (IBI) for robot tool path guide. By using image processing to process 2D drawings, image of actual parts or 3D models and using these references to input information to the VMD, allow the robot motion path to be generated automatically. These input type allows parts processing to be de-coupled from design driven automation machines. Where 3D models or some form of part reconstruction is required for computer aided manufacturing (CAM). With the on-board camera and image processing AI in the system, image of part is captured and compared against the translated image from the IBI.
The combination of the VMD and IBI provides many advantages to the manufacturing shop floor and the product owner.
1) Each process does not require product design details
a) Does not require an engineer to perform process/tool setup
b) Product owner IP is hidden from the shop floor / out-sourced workshop
c) Legacy infrastructure like CAD/CAM software and other compatibility issues
2) Minimal tooling required to setup process
3) Legacy product manufacturing can be quickly recovered
4) With feedback controls that are image based, adaptive AI can be integrated into automated process and act as a manufacturing execution system (MES), for process and quality controls.
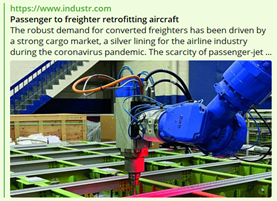
Boeing 767 Floor Grid Drilling
Passenger to freighter conversion
Robotic system with integrated motion & vision. Image feedback controls provide full feedback positioning on floating parts.
Deployed into production
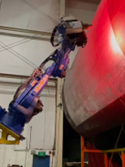
A321 Airframe Drilling
Cargo Door Retrofit
9-Axis robotic system with fully integrated motion & vision. Image feedback controls for positioning
Process feedback on positioning, incoming parts check, self alignment to fuselage surface
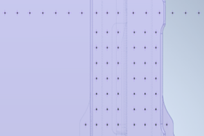
2D/3D Image Inputs for Robots
Helios proprietary drive system is able to accept legacy design information and convert information to robotic process motion
Minimizing efforts to digitize legacy industrial processes
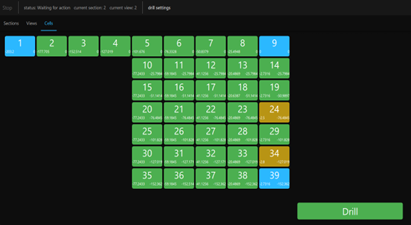
Process Co-Pilot
Robotic system could be integrated with process co-pilot
Provides real-time process feedback to end-user, includes alarm and feedback prompts if actual parts or process deviates from design rules
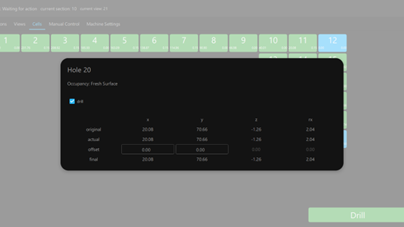
Manual Over-Ride
If abnormalities are detected during process and are within process tolerance, manual over-ride features will allow process modification
Audits and monitoring of incoming part and process design rules can be performed
Allows for AI feedback controls in the future
Same machine can perform re-work
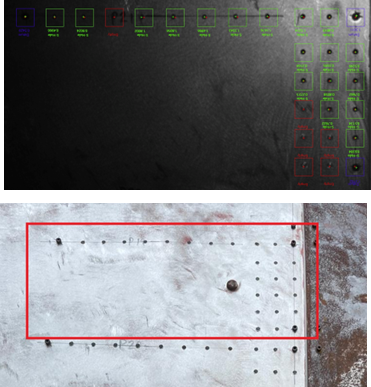
Vision Feedback
Live view of parts pre-processing
Information overlay on process areas, provides real-time inspection data compared against design rules